Mastering Electronic Expansion Valves: Installation and Diagnostics
Unlock precise refrigerant control by installing and troubleshooting electronic expansion valves. Learn advanced setup, calibration, and diagnostic steps for superior HVAC performance.
HVAC
3/24/20258 min read
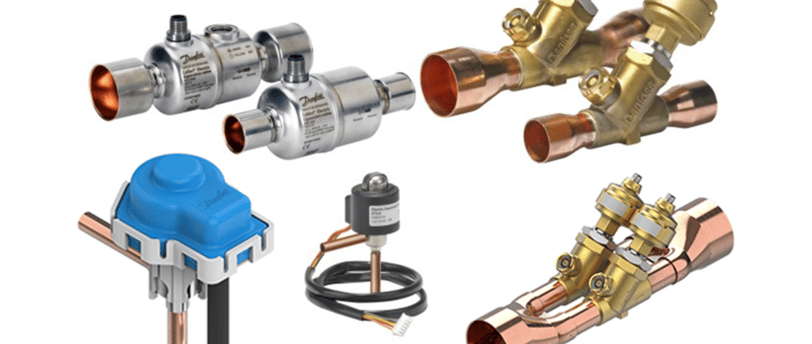
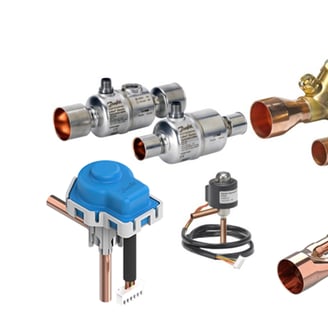
What This Post Covers
The unique role and advantages of electronic expansion valves (EEVs) in modern HVAC systems
Core components and how EEVs differ from traditional TXVs
Detailed installation tips and calibration best practices
Diagnostic steps for common EEV malfunctions
Practical, real-world examples of EEV commissioning
Pro-level guidance on ensuring reliable, efficient system operation
Support from SuperTech Industries for complex EEV challenges
Understanding the Rise of Electronic Expansion Valves
The expansion valve is integral to the refrigeration cycle, controlling how much liquid refrigerant enters the evaporator. Traditional thermostatic expansion valves (TXVs) respond to temperature and pressure changes mechanically; in contrast, electronic expansion valves (EEVs) leverage sensors and microprocessors for real-time fine-tuning. By rapidly adjusting orifice position through a stepper motor, EEVs offer greater precision—leading to improved energy efficiency, tighter superheat control, and smoother operation under varying loads.
Over the last decade, EEVs have become common in high-efficiency systems such as VRF (variable refrigerant flow) networks and advanced heat pumps. Their appeal lies not just in energy savings but also in more stable humidity management, quicker responsiveness to load changes, and comprehensive data collection for diagnostics. The complexity and cost of EEV systems, however, demand a deeper technical understanding—particularly during installation and troubleshooting. This post aims to equip you with the knowledge needed to install, calibrate, and maintain EEV setups at a high standard.
Why EEVs Matter in Modern HVAC
Precise Superheat Control: Rather than relying on a thermal bulb and spring mechanism, EEVs read multiple inputs (evaporator pressure, temperature sensors) to modulate refrigerant flow within seconds. They maintain an optimal superheat across a wide range of outdoor conditions or partial loads.
Energy Efficiency: By eliminating inefficiencies typical of mechanical valves, EEVs allow compressors to run closer to their ideal design conditions. In VRF systems, multiple indoor units can maintain distinct setpoints while the EEV fine-tunes each circuit’s refrigerant feed.
Rapid Adjustments: Mechanical TXVs sometimes lag when conditions shift abruptly—such as large occupancy changes or fast-moving weather fronts. EEVs respond faster, preventing overfeeding (flooding) or underfeeding (starvation) at the evaporator.
Data and Diagnostics: Many EEVs connect to advanced control boards or building management systems, providing real-time feedback on valve position, superheat, and alarms. This detail helps predict issues (like dirty coils, partial restrictions, or sensor errors) before they escalate.
Still, these benefits come with added complexity. Unlike a TXV that might survive minor installation mistakes, an EEV’s success hinges on correct wiring, sensor placement, and parameter configuration. Next, we’ll dive into how these valves actually function and what you need to know when integrating them.
Key Components and Principles of EEV Operation
Electronic expansion valves typically include:
Stepper Motor: Moves the valve pin in tiny increments (steps). Each partial rotation adjusts orifice size. The control logic pulses the motor coils with a precise sequence, letting it open or close in as many as several thousand steps.
Valve Body and Pin: The mechanical portion that physically restricts refrigerant flow. Machined tolerances are tight, so contamination can jam the pin.
Controller or Driver Module: Sometimes built into the system’s main control board, other times a standalone module. It receives inputs (e.g., evaporator temperature, suction pressure, superheat target) to compute the correct valve position.
Sensors: Thermistors or pressure transducers feed data back to the controller. Accurately installed sensors are paramount—if a temperature sensor is poorly insulated or placed incorrectly, superheat readings become skewed.
Closed-Loop Control
The essence of an EEV is closed-loop control: the system reads evaporator conditions (temperature, pressure, or superheat), compares them to the desired setpoint, and adjusts the valve’s step position accordingly. Each increment or decrement changes refrigerant flow, altering evaporator temperature and superheat in real time. A well-tuned system might hold superheat within a tight band (e.g., 5–7°F), optimizing evaporator efficiency without risking liquid carryover to the compressor.
Communication Protocols
In sophisticated systems (like VRF or multi-zone heat pumps), EEV driver modules communicate with a central controller through proprietary protocols. You might see addresses, DIP switch configurations, or network wiring that ensures each EEV receives instructions relevant to its zone. Mistakes in these settings can cause partial system malfunctions, with one indoor unit starved while another overfeeds.
Installation: Critical Steps for EEV Success
1. Proper Placement in the Refrigerant Circuit
Placing the EEV on the liquid line feeding the evaporator is standard. In some designs, you’ll find them near the outdoor unit; in others, closer to each indoor coil. Follow manufacturer diagrams precisely. Incorrect orientation or reversing inlet/outlet can cause erratic behavior or hamper the valve’s ability to regulate flow.
2. Cleanliness and Contamination Control
Because EEV orifices are smaller and more precise, any metal shavings, brazing flux residue, or dirt poses a risk of clogging. Good brazing technique—like flowing nitrogen through lines while brazing—and thorough system evacuation reduce contaminants.
3. Wiring and Connection
Each stepper motor typically has multiple leads. The control module or main board instructs coils in a specific sequence to rotate. Crossed wires can invert directions or jam the motor. Confirm color-coded wiring with brand-specific instructions. Loose or incorrect connections are a prime cause of EEV lockouts.
4. Sensor Placement
For robust superheat control, the system typically uses at least one temperature sensor on the evaporator outlet line and possibly a pressure sensor near the suction line. These must sit in stable, representative spots, firmly clamped and insulated from ambient air.
5. System Commissioning
Once physically installed, the next phase is programming. You’ll input or verify parameters like:
Evaporator design superheat (e.g., 5°F, 7°F, or other brand-specific defaults).
Minimum and maximum valve positions in steps.
Any defrost or auxiliary modes that require special EEV actions.
Time delays or control offsets to prevent oscillations.
Proper commissioning ensures the valve won’t overshoot or “hunt,” a phenomenon where it constantly opens and closes around the target superheat.
Diagnostics and Troubleshooting EEV Malfunctions
Symptom 1: Low Superheat or Floodback
If the compressor sees liquid refrigerant returning, it can damage internal parts. An EEV stuck too far open is one possibility.
Check Sensor Inputs: Are temperature or pressure sensors reading accurately? A dislodged sensor might report a higher temperature than actual, causing the valve to open more.
Verify Controller Settings: Improper superheat targets or reversed logic (like a DIP switch for “cooling only” set incorrectly) might lead to continuous overfeeding.
Valve Binding: If the valve’s stepper motor is physically stuck or contaminated, it may remain partially open.
Symptom 2: Excessive Superheat or Starved Evaporator
A coil that’s underfed can cause high superheat (10–20°F or more), reduced capacity, and potential compressor overheating.
Check Stepper Calibration: Some systems calibrate at startup, fully closing and re-establishing reference. If calibration fails, the valve might open fewer steps than needed.
Look for Voltage or Communication Errors: If the control board never commands the valve to open beyond a small number of steps, it suggests communication or sensor mismatch.
Physical Restriction: Kinks or partial blockages upstream can mimic an underfeeding EEV scenario. Confirm liquid line pressure is normal before suspecting the valve.
Symptom 3: Hunting or Rapid Cycling
A system that oscillates around the set superheat can short-cycle the compressor, degrade comfort, and wear out mechanical components.
Tuning the Control Loop: If the EEV’s PID (proportional-integral-derivative) or other control algorithm is poorly matched, you might see continuous over- and under-corrections. Some boards offer adjustable parameters to smooth out transitions.
Time Delays: Slight delays can prevent the valve from reacting too quickly.
Sensor Response Time: If the temperature sensor is too far from the evaporator exit, the feedback loop may lag, causing overshoot.
Symptom 4: Erratic Valve or Motor Errors
Some units store error codes if the stepper motor fails to respond or if coil windings read abnormal resistance.
Motor Coil Test: A typical stepper coil might read a certain ohm range (e.g., 160–220Ω). If open or shorted, the motor is toast.
Check Connectors: Pinched harnesses or loose connectors can cause intermittent control signals.
Firmware or Board Issues: In integrated systems, verifying the main firmware can matter—some manufacturers release updates to refine EEV control algorithms or fix known bugs.
Practical Case Study: Commissioning a Heat Pump with EEV
Picture a mid-sized heat pump where an installer just swapped from a TXV to an electronic expansion valve kit for better efficiency. Proper procedures might look like this:
Line Purge and Brazing: The technician flows nitrogen while brazing the valve assembly to keep the internal passages clean.
Mount the Controller: They attach the stepper driver board in the outdoor unit compartment, hooking up sensor leads to a dedicated harness.
Calibration: Upon initial startup, the EEV cycles fully closed, then fully open, establishing reference steps. The system’s control board displays “EEV Calibration OK.”
Check Superheat: They measure suction line temperature and evaporator pressure to confirm a superheat near the target (e.g., 5–7°F). If superheat is too high, they watch the valve open more steps. If it’s too low, the valve should close accordingly.
Log Data: Over 15–20 minutes, the system stabilizes. They note any rapid oscillations. If the valve hunts, the technician might adjust a control parameter limiting how quickly it changes positions.
Full Operating Range: They switch from mild weather settings to maximum load conditions, ensuring the EEV transitions smoothly without flooding or starved conditions.
Result: The heat pump runs more efficiently, especially in part-load conditions. Occupants notice more stable indoor temperatures and humidity control, and data logs show the compressor draws less amperage compared to the old TXV-based system.
Preventing Common EEV Pitfalls
Dealing with Power Interruptions: If the system experiences frequent short power cycles, the EEV might fail to recalibrate. Ensure your control board has a stable startup routine.
Cleaning the Refrigerant Circuit: After major service, a filter-drier or additional in-line filter is recommended to catch debris before it reaches the valve seat.
Sensor Integrity: Loose sensor clamps, frayed wires, or poor insulation degrade readings and confuse the EEV’s logic.
Beware of Low Ambient Conditions: Heat pumps operating in extreme cold must handle defrost cycles smoothly. EEVs might shift to specific positions during defrost. If code or parameter settings are wrong, expect frequent defrost misfires.
Follow Brand Procedures: Each manufacturer sets unique step counts, DIP switch options, or test modes. Skipping those instructions can create persistent nuisance faults.
When to Call a Professional
Installing or servicing EEVs often goes beyond typical mechanical instincts. The interplay of electronics, sensors, and programming demands a specialized skillset:
If you spot repeated error codes or partial motor movement, advanced diagnostic tools (like brand-specific software or proprietary harness testers) may be necessary.
For large commercial VRF systems or multi-zone setups, each indoor unit’s EEV must integrate with a master controller. A single misconfigured valve can disrupt the entire building’s climate control.
Any instance of shorted motor coils or damaged circuit boards typically needs brand-authorized parts and careful calibration. Attempting random replacements can worsen the issue.
SuperTech Industries has the expertise to handle EEV complexities—from routine installation to advanced multi-stage system troubleshooting. We keep your system streamlined so you reap the full advantages of modern refrigerant flow control.
Final Thoughts on EEV Mastery
Mastering electronic expansion valves means grasping more than just hooking up wires. You integrate mechanical, electrical, and refrigeration knowledge to achieve tight superheat control and system efficiency. Although the technology demands attention to detail—particularly with sensor placement, wiring harness integrity, and control algorithm tuning—the rewards are substantial: faster load response, better humidity regulation, and overall improved comfort.
No system, however, is foolproof. EEVs rely on crisp sensor feedback and stable power. They can jam with contaminants or misread superheat if you skip calibration or misinstall sensors. Thoroughly following each manufacturer’s guidelines, verifying stepper motor coil health, and practicing good brazing and cleaning keep issues at bay. Once dialed in, EEV-driven HVAC units often outlast older setups while delivering significant energy savings.
If you’re keen to upgrade from TXVs to EEVs or suspect an existing EEV setup isn’t performing as it should, don’t hesitate to seek expert input. “Don’t just call a tech, call a supertech.” At SuperTech Industries, our “Simple Solutions. Superior Results.” ethos ensures every detail—from sensor wiring to advanced firmware settings—is fine-tuned for top-tier system performance. Let us help you tap the full potential of electronic expansion valves, freeing you from subpar superheat control and ushering in a new era of HVAC efficiency.
SuperTech Industries
Your trusted partner for all your solutions.
KNOWLEDGEABLE - AFFORDABLE - ADAPTABLE - DEPENDABLE
© 2024. All rights reserved.